Navigating Vehicle Breakdowns With Fleet Management Solutions
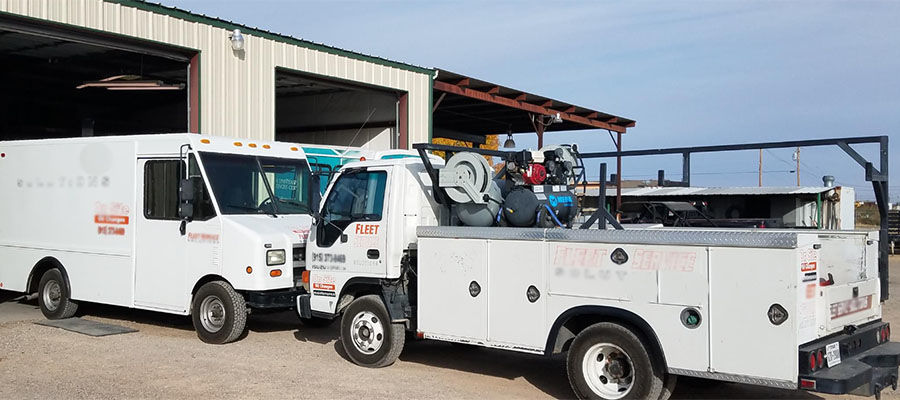
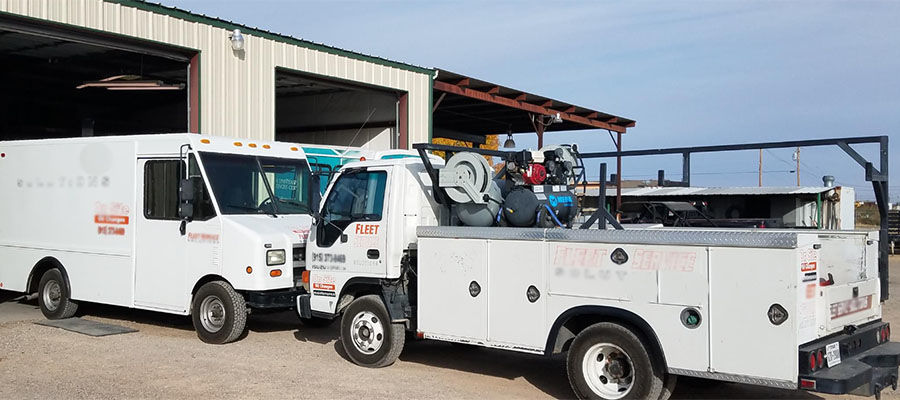
Navigating Vehicle Breakdowns With Fleet Management Solutions
Meeting deadline agreements is a keystone of professionalism, be it in construction, industrial sectors, delivery services, or any other business. For many business owners and managers, that means one or more work trucks or vans must be in the field and on time. But even with the most diligent preventive maintenance, commercial vehicle breakdowns are bound to occur. Fleet management solutions offer a strategic approach to managing these unforeseen challenges.
The Significance of Deadline Adherence
Not meeting contract deadlines can lead to heavy financial losses, damage to reputation, and even legal consequences. A delay can create a domino effect, impacting stakeholders like clients, subcontractors, and suppliers, often culminating in a loss of trust and credibility. Being on time reflects on an organization's efficiency, reliability, and commitment to its stakeholders.
Reputational
In a world connected by instant communication and social media, news of a company failing to meet its commitments can spread rapidly. This can significantly tarnish its reputation. For businesses, reputation is a valuable intangible asset. Once damaged, it requires significant time and resources to rebuild, if it can be restored at all.
Financial
Missing deadlines has financial implications that can lead to a chain reaction of monetary consequences. Companies may face penalties for late deliveries or project completions. Additionally, prolonged delays might result in compensation or even breach-of-contract lawsuits. Such financial setbacks can greatly affect a company's bottom line and whether it’s included in future ventures.
Legal
Beyond financial penalties, not meeting deadlines, especially in sectors with stringent regulatory guidelines, can lead to legal actions. Such legal battles not only drain resources, but can also lead to business licenses being revoked or further scrutiny from regulators.
The Domino Effect
Deadlines often interlink various stakeholders in a project's lifecycle. A delay in one phase can have cascading effects on subsequent phases. For instance, a delay in delivering construction materials can push back the timelines for subcontractors responsible for installation. This can further impact suppliers waiting to provide finishing products. Such a ripple effect can exponentially increase the costs and complexities of project management.
In sum, deadline adherence is more than just punctuality—it's a testament to a company's operational efficiency, commitment to stakeholders, and its place in the competitive market landscape. Delays, no matter how minor they seem, can amplify challenges and setbacks, making them a crucial area of focus for businesses.
The Inevitability of Breakdowns
Modern commercial vehicles, with their intricate systems, aren't immune to mechanical failures even with rigorous maintenance.
Complexity
The progression of automotive engineering has given rise to commercial vehicles that are marvels of modern technology. These vehicles, equipped with complex systems and cutting-edge components, are designed to maximize efficiency, safety, and comfort. However, this intricacy comes with a commensurate maintenance challenge. As vehicles evolve, they incorporate advanced electrical systems, computerized components, and state-of-the-art machinery. Each element, while contributing to the vehicle's overall performance, is also a potential point of failure. With numerous interconnected systems, a fault in one can sometimes lead to cascading issues in others.
Wear and Tear
No matter how advanced a vehicle is, it's still subjected to the natural wear and tear of regular use. And even the simplest vehicle can throw a curveball now and then. Factors like road conditions, weather extremes, and heavy-duty usage can exacerbate this wear, leading to the premature aging of certain components.
Limitations of PM
While regular maintenance can identify and rectify many potential issues, it's not foolproof. Some failures occur without warning, driven by unpredictable factors or latent defects. Furthermore, as vehicles become more technologically advanced, their maintenance requires specialized skills, tools, and knowledge, which might not always be readily available. Despite preventive measures, unexpected breakdowns are a consistent concern across sectors, from logistics and transportation to construction and delivery services.
Despite our best preventive efforts, the inevitability of breakdowns underscores the importance of robust response strategies and advanced fleet management solutions.
Using Fleet Management Solutions To Mitigate Downtime
Fleet management solutions, an amalgamation of sophisticated software and hardware, provide real-time insights into equipment health. Fleet management software such as Fleetio, Samsara, and Teletrac Navman, vary in complexity, price, and capabilities. Although their predictive analytics capability can flag potential issues before they become critical, they also have a significant capability to be utilized for a rapid response to the inevitable on-the-job breakdowns.
Enhancing Communication Between Technicians
Effective communication between in-shop and on-road technicians is a challenge. Fleet management tools offer centralized platforms that promote transparent and seamless information sharing. Integrated mobile apps and IoT devices are key in ensuring rapid response to breakdowns.
For commercial vehicles that break down during work, an effective rapid response that ensures the job gets done in a timely manner would involve the following steps and elements:
- Immediate Notification: As soon as a vehicle breaks down, the driver or an onboard monitoring system should instantly notify the central platform about the breakdown.
- Diagnostics and Data Collection: IoT devices can provide real-time diagnostic information on what went wrong with the vehicle. This information is crucial for the on-road technician to prepare and bring the right tools and parts.
- Location Sharing: The exact location of the broken-down vehicle can be shared with on-road technicians via GPS, enabling them to reach the site faster.
- Assignment of On-Road Technicians: The fleet management platform can automatically assign the nearest available on-road technician to address the breakdown, reducing response time.
- Mobile Apps for Technicians: Technicians should have access to mobile apps that provide them with:
- Detailed information about the breakdown.
- Previous maintenance records of the vehicle.
- Communication channels to speak directly with the driver or in-shop technicians.
- Navigation to the breakdown location.
- Ability to update the status of the repair in real time.
- Spare Parts Inventory: If the breakdown requires replacement parts, the system should quickly identify the nearest inventory location. This can either be from a nearby service vehicle or a nearby service center.
- Triage System: Not all breakdowns are of the same priority. Having a triage system in place helps in prioritizing breakdowns based on severity, ensuring that vehicles with critical issues get attended to first.
- Communication Channels: In addition to the mobile apps, there should be a robust communication channel (like push-to-talk radios or integrated chat systems) that allows in-shop technicians, on-road technicians, drivers, and fleet managers to collaborate and share information.
- Feedback Loop: After the repair, feedback should be gathered from the driver and the technician. This feedback can be used to continuously improve the rapid response process.
- Training and Drills: Regular training and mock drills can ensure that every team member knows their role and responsibilities in case of a breakdown. This will further speed up the response and repair times.
By integrating these elements and following the above steps, commercial vehicle fleets can ensure a rapid and efficient response to breakdowns, minimizing downtime and ensuring smooth operations.
Future Trends in Downtime Mitigation
The horizon of downtime mitigation is promising, with emerging technologies like AI-driven maintenance and remote diagnostics. The marriage of automation and enhanced connectivity will only solidify the prowess of fleet management solutions.
In the dynamic world of business, challenges like vehicle breakdowns are inevitable. However, with the right tools, notably fleet management solutions, their impact can be minimized. As technology continues to evolve, its role in ensuring that contract deadlines are consistently met, irrespective of unforeseen challenges, will only grow in prominence.
Published on: October 03, 2023Winterizing Commercial Vehicles: Don't Get Caught Out in the Cold!
Navigating Your Options: Key Tips For Choosing The Right Commercial Vehicle
Routeway 360 and Comvoy Launch Portal so Independent Distributors Can Find Suitable Work Trucks
Easing Into a Zero-Emission Commercial Vehicle Fleet: How One Hydrogen Truck Can Start a Revolution
Class 2b-3 Commercial Vehicles: How the Industry Can Find the Right Balance Across Supply, Demand, and Emissions Requirements